EVA Plastic Slippers
We are a Chinese company mainly for home and outdoor slippers. With an extensive factory resources, it is easy for us to offerbelow service
- low MOQ - even 200 pieces
- short L/T- 7 days
- free design - logo & pattern printing
Why Choose us?
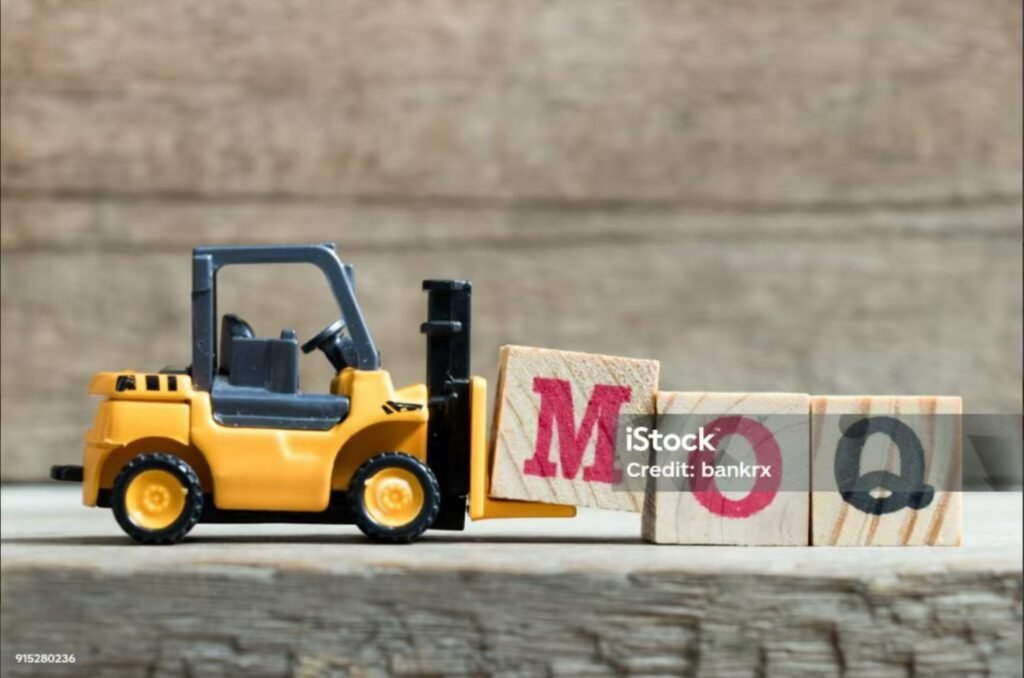
Low MOQ
Small MOQ is available and you can purchase different types in one batch
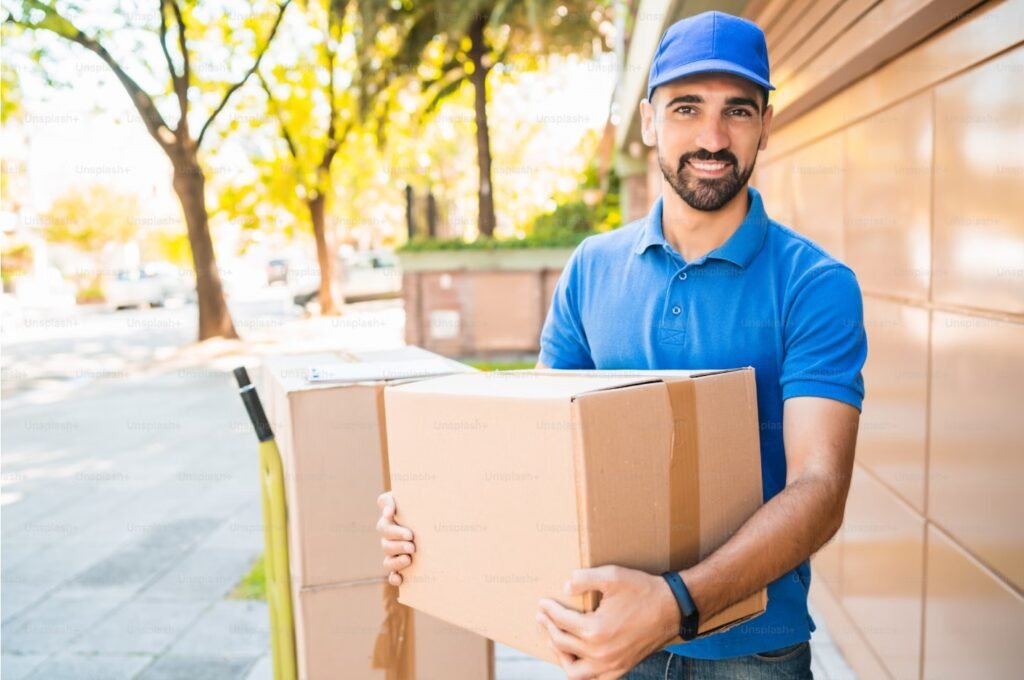
Fast Delivery
We’re so confident in our slippers that we offer a 7-15 day lead time on all orders.
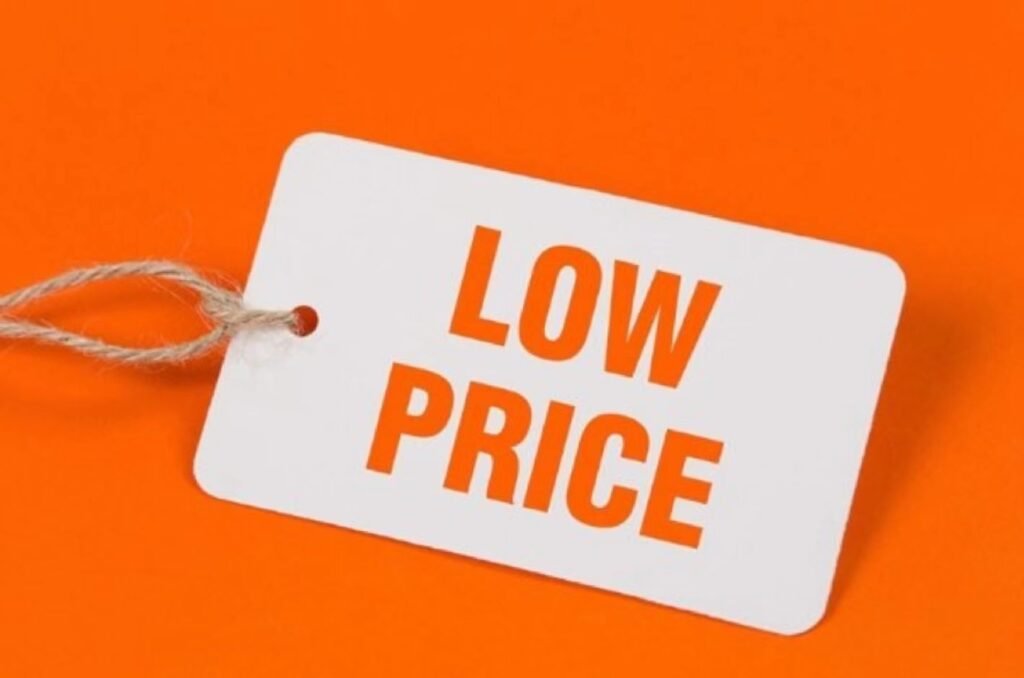
Competitive Price
We always provide high-quality slippers at an affordable price.
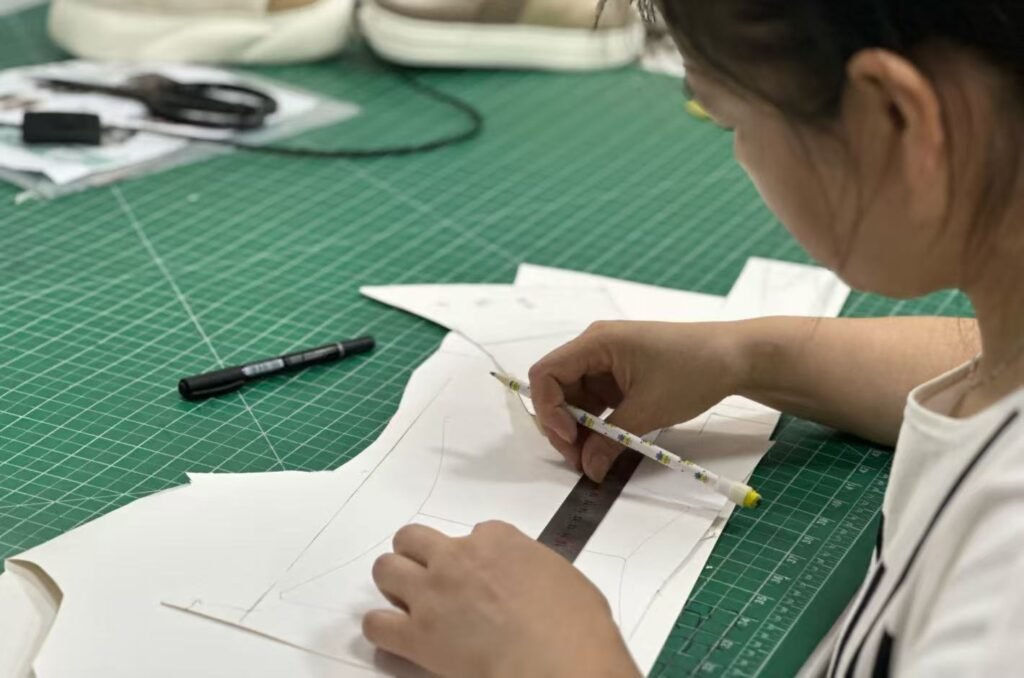
OEM/ODM
We have a team of experts who can help you find the perfect solution for your needs.
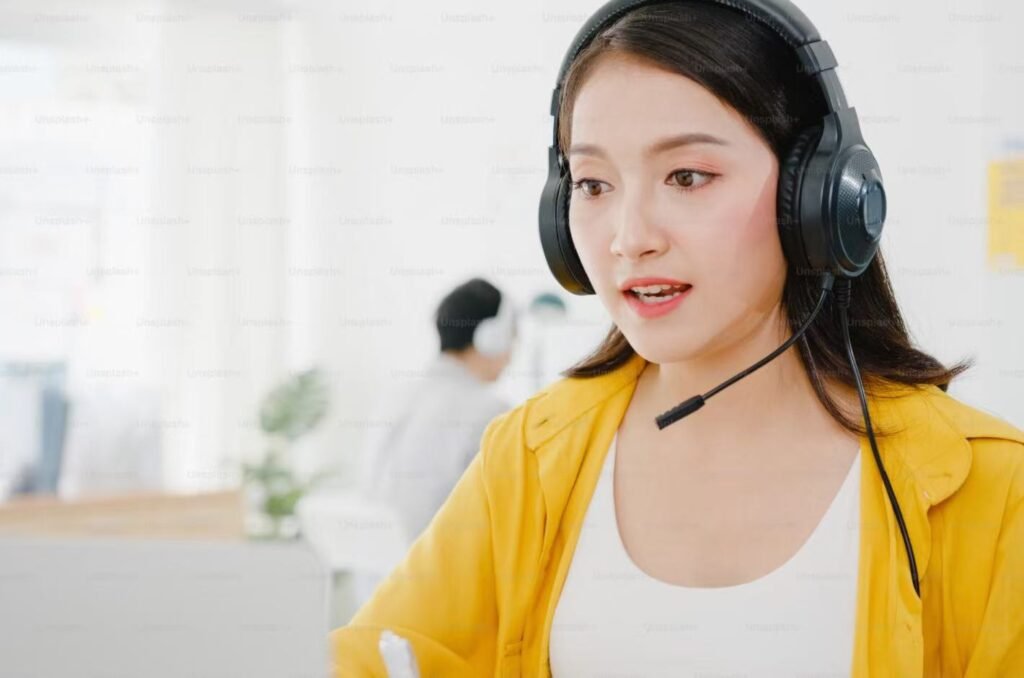
Customer Service
We’ll get you the answers to all of your questions, quickly and effectively
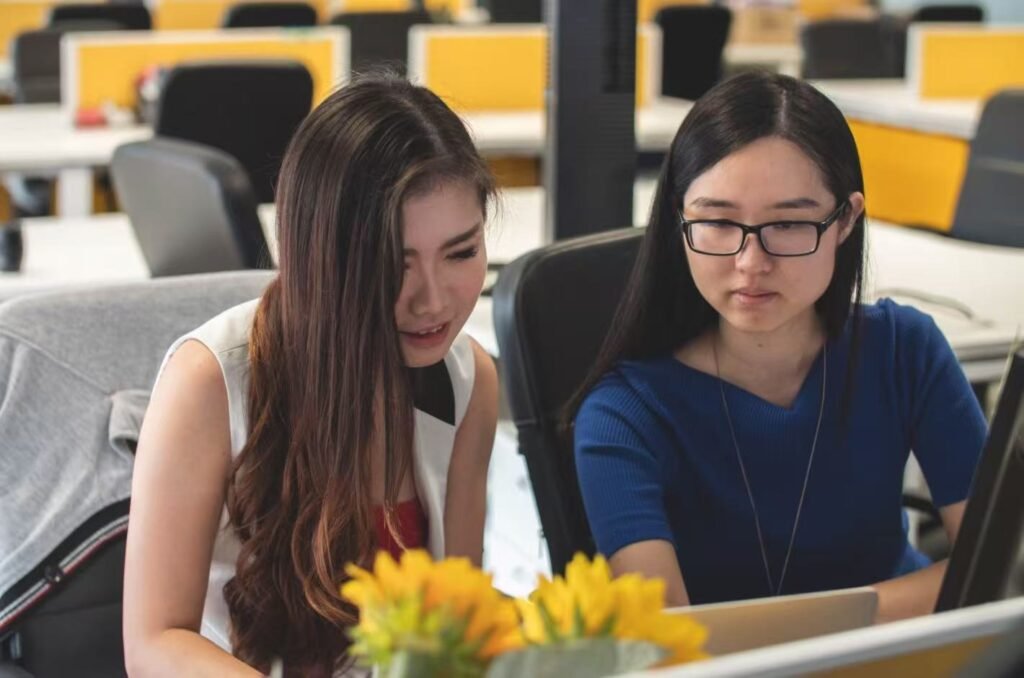
Easy Communication
We think in your ways. Consider your requirements in priority and how to meet them.
100+ Knowledge You Need to Know About EVA Plastic Slippers
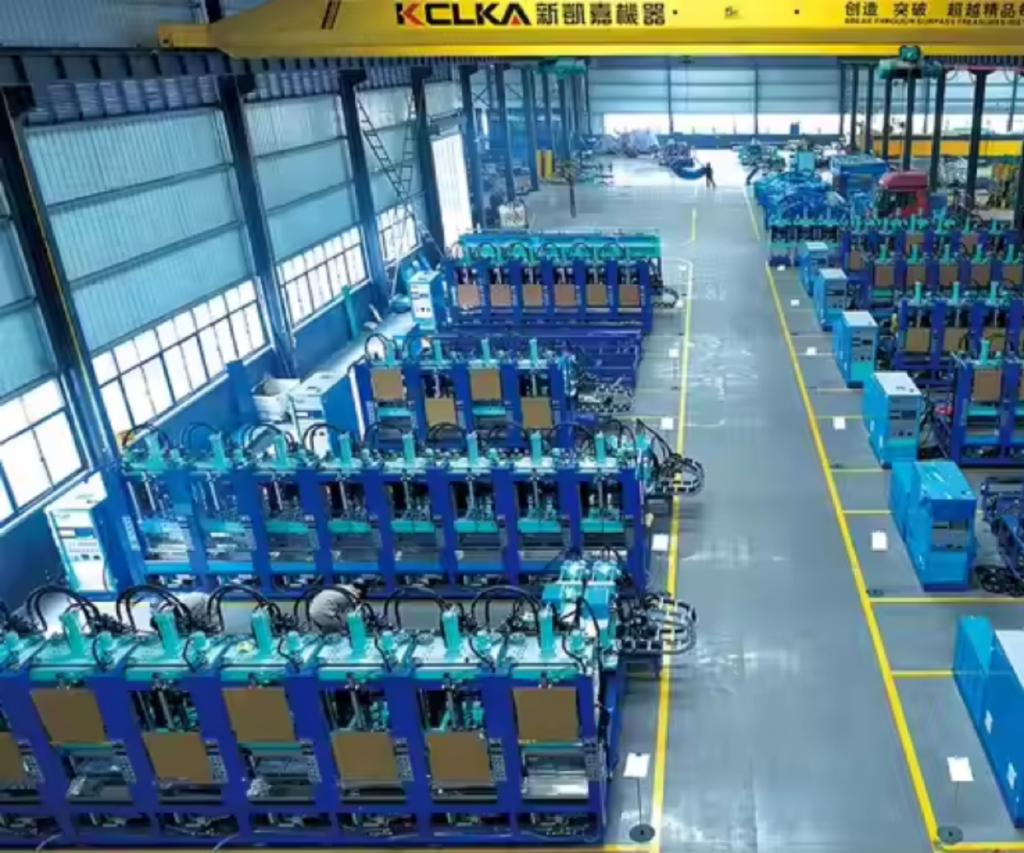
Production process
What are the common production methods of EVA slippers?
1.Injection Molding: Suitable for mass production, the shape and thickness of the slippers are relatively uniform, and complex designs can be achieved.
2.Compression Molding: It is suitable for producing thicker slippers, especially for manufacturing midsoles or soles.
3.Extrusion Foaming: This allows for the production of lightweight, flexible materials, and is commonly used in the soles of slippers.
4.Foaming Molding: Used to produce EVA slippers with a foam structure, usually used for soles of casual or lightweight styles.
5.Injection Compression Molding: Suitable for producing EVA slippers with complex shapes, especially the sole part.
6.Cutting and Lamination: Suitable for producing simpler slipper styles, usually used for producing flat slippers.
7.Rolling Foaming Molding: Can produce uniform foamed products, the material has good softness and elasticity.
What kind of slippers are suitable for the above process?
1.Injection Molding: Suitable for slippers with complex structures and more design details, such as sandals, sports slippers, children’s slippers, etc.
2.Compression Molding: It is suitable for slippers that require higher elasticity and good shock-absorbing performance. It is often used in shoes with thicker or elastic soles, such as sports slippers, outdoor slippers, and sandal soles.
3.Extrusion Foaming: It is suitable for producing light, soft and comfortable slipper soles, mainly used in home, light slippers or foam beach slippers.
4.Foaming Molding: It is suitable for producing lightweight, elastic and soft casual slippers, especially shoes with strong foam texture, such as beach slippers, home slippers, indoor slippers, etc.
5.Injection Compression Molding: Suitable for slippers with complex structures and high requirements on details and precision, such as fashion sandals, sports slippers, etc.
6.Cutting and Lamination: Suitable for slippers with simple structure and single design, such as flat slippers, indoor slippers, hotel slippers, etc.
7.Rolling Foaming Molding: It is suitable for the production of slippers that require large-area foaming materials, usually used for home slippers, sports insoles or soles.
How do different production processes affect the quality and performance of EVA slippers?
1. Injection Molding
High appearance and detail precision Injection molding can produce slippers with complex shapes and precise details, suitable for high-precision design and styles with rich decorative details.
Good consistency: The slippers produced by injection molding have stable quality, uniform shape and size, and reduce the occurrence of defects.
Strong durability: The injection molding process can control the density and hardness of the material, making the slippers more wear-resistant and suitable for daily wear.
Medium comfort: Due to the high density of the injection molding material, the elasticity of the slippers is relatively low, the sole may be slightly harder, and the comfort is lower than the slippers produced by the foaming process.
2. Compression Molding
High elasticity and shock absorption: EVA slippers produced by compression molding tend to have a higher density, good sole flexibility, better elasticity, and can provide good sole support and shock absorption.
Strong wear resistance: Due to the use of high-pressure molding, the sole material is denser, which increases the wear resistance and deformation resistance of the slippers.
Good durability: The soles of slippers produced by compression molding are usually thicker, suitable for frequent wear and long service life.
Less complex design: Due to process limitations, the complex design and details of the shoes are not as fine as injection molding, and are suitable for medium-complexity soles or uppers.
3. Extrusion Foaming
Lightweight and comfortable: The bubbles generated during the foaming process make the material very light, so the slippers are light and comfortable to wear.
Good softness: The extrusion foaming process makes the EVA material elastic and soft, suitable for shoes with high requirements for lightness and comfort.
Good cushioning performance: The foaming structure gives the sole a good shock-absorbing effect, suitable for home and leisure wear.
Medium durability: Due to the loose foaming structure, the material has low wear resistance and impact resistance, and it is easy to wear out after long-term wear.
4. Foaming Molding
Excellent comfort and lightness: Foaming EVA slippers are lightweight and soft, making them very suitable for long-term daily wear, especially for shoes that need to be light and comfortable.
Good cushioning effect: Foaming slippers can provide good cushioning effect, reduce foot pressure, and are suitable for home and leisure use.
Low wear resistance: Similar to extrusion foaming, foaming slippers are soft but have poor wear resistance and are prone to wear after long-term wear.
General surface finish: Due to the foaming process, the surface is usually rough, which is suitable for shoes that do not emphasize the fineness of the appearance.
5. Injection Compression Molding
Combines the advantages of injection molding and hot pressing: The injection compression molding process can produce slippers that have both the fine appearance of the injection molding process and the high elasticity and good shock absorption performance of the hot pressing process.
Complex structure and durability: This process is suitable for manufacturing slippers with multi-layer structures or complex designs. The soles are usually more wear-resistant and have good elasticity.
Stable performance: The finished product has good consistency and high dimensional accuracy, which is suitable for mass production of high-quality slippers.
Good comfort: The sole has good elasticity and is suitable for slipper styles that require support and comfort.
6. Cutting and Lamination
Low production cost: Cutting and lamination is a simple process, suitable for low-cost mass production, and is often used to make disposable or simple slippers.
Softness and elasticity depend on the material: The comfort, softness and elasticity of the slippers mainly depend on the quality of the EVA foam material used, and the performance of the finished product varies greatly.
Simple structure and wide applicability: The process is simple and suitable for making basic flat slippers, but due to the lamination, the delamination problem between the sole and the upper may occur.
7. Rolling Foaming Molding
Good material uniformity: The rolling foaming process can produce EVA materials with uniform density, ensuring the thickness consistency of the sole, and good comfort and shock absorption performance.
Soft and comfortable: The soles of slippers are usually softer, suitable for shoes with high comfort requirements.
Moderate wear resistance: The material is uniform and suitable for long-term wear, but the wear resistance of foam materials is still not as good as that of hot press molding products.
#What Are the Pros and Cons of Compression Molding vs. Injection Molding?
1. **Compression Molding**
– **Pros**: Lower cost, good elasticity, suitable for complex shapes and layered structures.
– **Cons**: Lower production efficiency and detail precision.
2. **Injection Molding**
– **Pros**: High precision, fast production, minimal material waste.
– **Cons**: Higher initial cost, lower elasticity.
How Do the Production Cycle and Output Efficiency of Compression Molding vs. Injection Molding Compare?
1. **Compression Molding**
– **Production Cycle**: Longer cycle due to slower heating and cooling.
– **Output Efficiency**: Lower, more manual operation.
– **Best For**: Small-batch, customized production with complex shapes.
2. **Injection Molding**
– **Production Cycle**: Short cycle with high automation.
– **Output Efficiency**: High, ideal for rapid mass production.
– **Best For**: Large-scale production with high precision and consistency.
Are There Automated Production Systems to Improve Manufacturing Efficiency?
1. **Automatic Injection Molding Machines**
– **Benefit**: Reduces manual intervention with precision control for high-volume, consistent production.
2. **Automated Compression Molding Machines**
– **Benefit**: Controls heating/pressing for uniform shaping; ideal for small-batch, elastic products.
3. **Smart Assembly Line Systems**
– **Benefit**: Integrates production stages with conveyor and robotic systems for full automation and rapid output.
4. **Intelligent Quality Control Systems**
– **Benefit**: Uses AI for defect detection, ensuring consistent quality and reducing rework time.
5. **Automated Material Mixing Systems**
– **Benefit**: Ensures precise ingredient mixing, reducing waste and improving batch uniformity.
What Impact EVA Slipper Production Costs?
1. **Raw Materials**
– **EVA Quality**: Higher-density, durable EVA increases material costs.
– **Additives**: Enhancements like dyes or anti-aging agents add to expenses.
– **Composite Materials**: Using rubber or leather for added functionality raises costs.
2. **Key Processes**
– **Molding Choice**: Injection molding suits mass production but has high initial mold costs; compression molding is slower but cheaper for small batches.
– **Heating and Cooling**: High-energy consumption during frequent heating/cooling impacts costs.
– **Assembly and Finishing**: Manual assembly steps add labor costs, especially in custom designs.
3. **Equipment**
– **Mold Costs**: Precision molds are costly, especially in injection molding.
– **Automation**: Machines like automatic injectors and smart lines boost efficiency but require high initial investment.
– **Quality Control Systems**: Automated inspection lowers defect rates but adds to equipment expenses.
How to Effectively Reduce Defect Rates and Waste to Save Costs?
1. **Automated Quality Control Systems**
– **Benefit**: Real-time detection reduces defects early, minimizing rework and material waste.
2. **Optimized Mold Design**
– **Benefit**: High-precision molds improve product consistency, lowering defect rates and material usage.
3. **Accurate Material Mixing with Automation**
– **Benefit**: Precise automated mixing reduces material waste and ensures product quality.
4. **Standardized Process Parameters**
– **Benefit**: Consistent monitoring of temperature, pressure, etc., stabilizes quality, reducing defects.
5. **Waste Recycling and Reuse**
– **Benefit**: Recycled scraps cut raw material costs and waste disposal expenses.
6. **Employee Training for Quality Awareness**
– **Benefit**: Skilled staff minimize operational errors, lowering defect rates and material wastage.
How to Ensure Consistency in Density, Color, Elasticity, and Surface Smoothness Across EVA Slipper Batches?
1. **Precise Material Ratio Control**
– **Benefit**: Automated mixing minimizes human error, ensuring stable density and color across batches.
2. **Standardized Production Parameters**
– **Benefit**: Consistent temperature, pressure, and heating time maintain uniform elasticity and finish.
3. **Color Consistency Management**
– **Benefit**: Pre-production color testing aligns color intensity, preventing batch-to-batch color variation.
4. **High-Precision Molds and Surface Maintenance**
– **Benefit**: Quality molds and regular maintenance ensure smooth, uniform surfaces on all products.
5. **Batch Quality Testing and Feedback**
– **Benefit**: Regular batch testing detects variations early, guaranteeing consistent quality standards.
Slippers Material
How to Maintain Elasticity and Deformation Resistance in EVA Material
1. **Optimize Formulation**
– Adjust the ratio of ethylene and vinyl acetate (VA) to enhance elasticity and compression resistance.
– Add antioxidants and UV stabilizers to slow down aging.
2. **Control Foaming Density**
– Choose an appropriate foaming density to balance elasticity and anti-compression properties.
– Adjust foaming density according to the usage scenario for improved durability.
3. **Appropriate Post-Processing**
– Use secondary heating or anti-compression techniques to stabilize the internal structure.
– Heat treatment can relieve internal stress and reduce compression deformation.
4. **Daily Maintenance and Usage**
-Don’t let it get squished for long periods of time. Make sure it getspressed evenly
-Don’t let it get too hot or exposed to strong UV.
5. **Advanced Modification Techniques**
-Blend it with something else (like TPE) to make it more elastic and moreresistant to deformation.
How EVA Elasticity Affects Comfort and Long-Term Wear
1. **Enhanced Shock Absorption for Comfort**
-EVA is elastic, which means it’s good at cushioning and reducing the impact between your foot and the ground.
-This is great for walking, running, or standing because it helps reduce foot fatigue.
2. **Reduces Foot Pressure**
-It spreads out the pressure on your foot so you don’t have one spot getting all the pressure. This makes your foot feel better.
-It supports your foot all the way across, so you don’t get tired or sore in one spot.
3. **Durability Supports Long-Term Comfort**
– Good quality EVA doesn’t get squished down and lose its elasticity over time.
4. **Adaptability to Various Environments**
– EVA is stable in extreme conditions (like temperature and humidity). This means it feels good in all kinds of weather.
– EVA stays soft in cold or damp environments, so it feels good when you wear it for a long time.
5. **Fatigue Prevention**
– EVA’s elasticity reduces foot fatigue compared to less elastic materials.
– Especially beneficial in prolonged standing scenarios, reducing strain on feet and legs.
Does EVA have good wear resistance?
1. **Abrasion Resistance**
– EVA has moderate abrasion resistance, suitable for light use environments.
-It’s not as good as rubber when you rub it on rough surfaces. If you use it outside a lot, it will wear out faster.
2. **Ideal for Indoor and Light Outdoor Use**
– It’s great for indoor slippers because it’s durable enough on smooth floors.
– If you’re going to use it outside a lot on rough surfaces, you might need to combine it with rubber to make it last longer.
3. **Lightweight and Comfortable**
– EVA is light and elastic, which makes it feel good when you wear it for a long time.
-It’s light, so it feels better to wear in the house than something heavy like rubber.
4. **Durability and Cost-Effectiveness**
– EVA is cheap and lasts a pretty good amount of time for indoor slippers
– If you’re going to use it in a place where it gets rubbed on a lot, it might not be enough by itself.
5. **Enhanced Options with Composite Materials**
-You can combine EVA with rubber or other stuff to make it last longer
How Does EVA Material's Lightweight Affect Slipper Design and Functionality
1. **Reduces Foot Load and Increases Flexibility**
– Because it’s light, you can make your slippers more flexible. This is great for sports or functional slippers because it doesn’t get in the way of moving your feet.
2. **Impact on Support**
– It’s light, but it’s not going to support your foot like a high-arch or super supportive thing.
– It’s good enough for basic support and cushioning in normal slippers, but you might need to add something else if you want a lot of support.
3. **Trade-Offs in Anti-Slip Design**
-It doesn’t grip as well as rubber. You can make it grip better by adding some rubber on the bottom or by making the bottom have a texture.
– It’s good enough to keep you from slipping on normal floors, but it’s not as good as something heavier if you’re walking around on wet stuff.
5. **Balancing Lightweight with Durability**
– It’s great for travel or everyday slippers. It’s not going to last as long as other stuff if you use it a lot.
– You can combine it with other stuff to make it last longer if you’re going to use it in a place where it gets rubbed on a lot.
How does EVA material help slippers to be non-slip?
1. **Natural Friction of EVA**
– EVA provides basic anti-slip through natural friction, suitable for dry, flat surfaces.
2. **Textured Design for Improved Grip**
– Sole patterns (e.g., wave or stripe textures) increase contact area, enhancing slip resistance, especially on dry surfaces.
3. **Composite Materials for Enhanced Wet Traction**
– EVA combined with rubber soles improves grip on wet surfaces, balancing lightweight with increased anti-slip properties.
4. **Drainage Channels for Wet Conditions**
– Drainage grooves in the sole help expel water, reducing the risk of slipping in damp environments like bathrooms.
Is EVA Material Water-Resistant?
Yes!
1. **Low Water Absorption**
-EVA is closed-cell structure, so it doesn’t absorb water. That’s why it stays light and bouncy even when it’s wet.
2. **Quick-Drying**
– Dries quickly after contact with water, minimizing odor and bacterial growth, ideal for use around pools, beaches, and showers.
3. **Suitable for Anti-Slip Designs**
-It works great with drainage channels or textured soles to give you better traction. That’s why it’s so durable in wet environments.
4. **Easy to Clean and Maintain**
-It doesn’t absorb water, so you can easily wash it. It doesn’t grow mold, either. That’s why it’s perfect for places where you have to clean a lot.
Is EVA Material Easy to Shape and Color?
1. **Easy Shaping for Diverse Designs**
– EVA is highly moldable, allowing for various shapes and contours that enhance comfort and style.
2. **Wide Range of Color Options**
-It takes color great. That’s why you can get it in so many different colors. It doesn’t fade, either.
3. **Supports Creative and Functional Enhancements**
-You can use it with other materials to make it last longer or to give it a better grip. That’s how you make ergonomic, functional designs.
4. **Cost-Effective for Mass Production**
– Simple processing and low costs make it ideal for large-scale, affordable production, allowing rapid response to trends.
Can EVA Be Combined with Other Materials to Enhance Slipper Functionality and Aesthetics?
1. **Rubber**
– Adding a rubber layer enhances grip, ideal for wet or slippery surfaces while keeping EVA’s lightweight quality.
2. **Fabric **
– Combining with breathable fabrics enhances comfort and style, perfect for summer wear.
3. **Leather**
– Leather or faux leather adds a premium look, blending style with EVA’s softness.
4. **Hard Materials**
– Integrating TPU or similar materials increases support, beneficial for prolonged wear.
Is EVA Material Eco-Friendly and Safe for Human Use?
1. **Non-Toxic and Safe**
– EVA is generally free from harmful chemicals like phthalates, making it safe for human contact.
2. **PVC-Free**
– As a PVC alternative, EVA doesn’t produce dioxins or other persistent pollutants during production.
3. **Limited Biodegradability**
– Not easily biodegradable, which can impact the environment if not properly managed.
4. **Meets Environmental Standards**
– High-quality EVA complies with standards like ROHS and REACH, ensuring safety in consumer products.
How to Assess the Environmental Impact of EVA Slippers
1. **Production Process Impact**
– Evaluate energy use and emissions in EVA production, favoring low-energy, low-waste methods.
2. **Degradability and Recyclability**
– Assess EVA’s biodegradability and potential for recycling, as it is challenging to decompose naturally.
3. **Durability and Lifespan**
– Longer-lasting EVA products reduce waste by decreasing replacement frequency.
4. **Waste Management and Reuse**
– Consider recycling options and reuse programs for discarded EVA products to minimize landfill impact.
5. **Environmental Certifications**
– Choose EVA products meeting standards like ROHS and REACH to ensure reduced environmental and health risks.
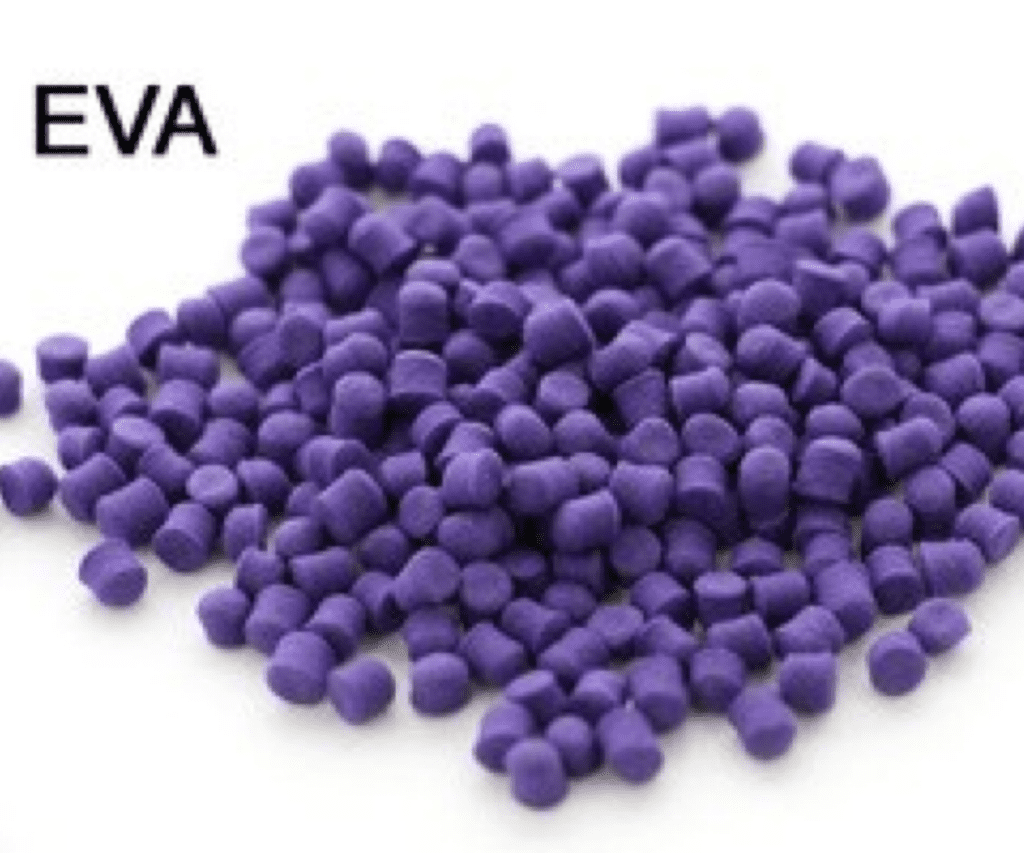
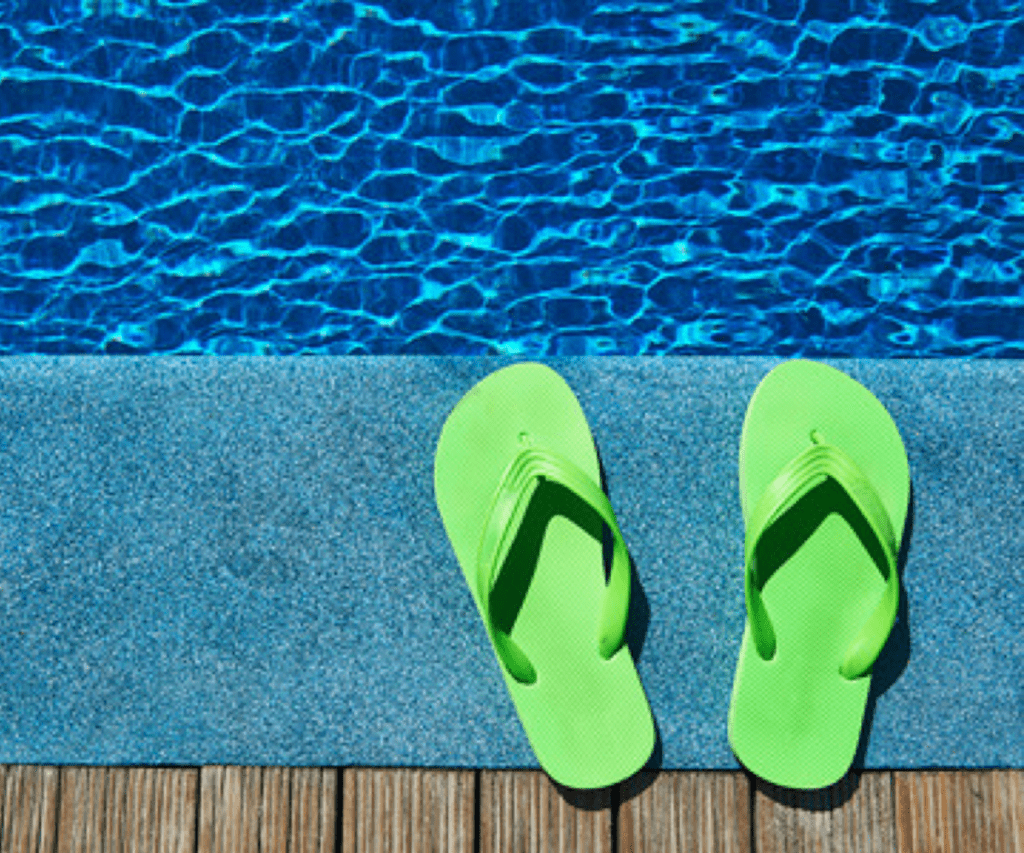
Application scenarios
What Factors Do Household Users Prioritize When Choosing EVA Slippers?
1. **Comfort**
– **Focus**: Good elasticity, cushioning, and a soft footbed for long-term wear.
2. **Anti-Slip**
– **Focus**: Effective sole grip, especially for wet areas like bathrooms.
3. **Durability**
– **Focus**: Resistance to wear and deformation for prolonged use.
4. **Easy to Clean**
– **Focus**: Waterproof and low-maintenance, with some opting for antibacterial features.
5. **Aesthetics**
– **Focus**: Appealing colors and designs that match home decor.
6. **Cost-Effectiveness**
– **Focus**: Good balance of price and quality for long-term value.
What Are the Primary Requirements for Bathroom Slippers?
1. **Anti-Slip**
– **Focus**: Effective grip on wet surfaces to prevent slipping.
2. **Waterproof and Quick-Drying**
– **Focus**: Non-absorbent material that dries quickly to prevent bacteria growth.
3. **Easy to Clean**
– **Focus**: Smooth, stain-resistant surface for simple rinsing.
4. **Comfort**
– **Focus**: Cushioning and support for soft, comfortable wear on wet floors.
5. **Antibacterial Properties**
– **Focus**: Antimicrobial design to reduce odor and maintain hygiene.
What are Considered for EVA Slippers in Outdoor Settings (Beach, Pool, Gym)?
1. **Anti-Slip**
– **Focus**: Enhanced grip for wet and slippery surfaces.
2. **Durability and Abrasion Resistance**
– **Focus**: High-density EVA or rubber layers for wear on rough surfaces.
3. **Waterproof and Quick-Drying**
– **Focus**: Non-absorbent, fast-drying material to prevent moisture buildup.
4. **Lightweight**
– **Focus**: Easy to carry and comfortable for extended wear.
5. **UV and Wear Resistance**
– **Focus**: Materials resistant to sun and abrasion for long-lasting use.
6. **Comfort and Support**
– **Focus**: Cushioning and arch support for comfort on varied surfaces.
What Are the Primary Target Markets for EVA Slippers?
1. **Household Users**
– **Focus**: Comfort, anti-slip, and easy cleaning for home and bathroom use.
2. **Travel and Outdoor Enthusiasts**
– **Focus**: Lightweight, waterproof, and portable for beach, pool, and camping activities.
3. **Fitness and Sports Enthusiasts**
– **Focus**: Durability, anti-slip, and quick-drying for gym and pool settings.
4. **Hotels and Hospitality**
– **Focus**: Cost-effective, hygienic, and easy-to-clean slippers for guest use.
5. **Medical and Care Facilities**
– **Focus**: Anti-slip, antibacterial, and hygienic for hospital and nursing home environments.
6. **Fashion and Casual Consumers**
– **Focus**: Style, design, and variety for everyday casual and fashion-forward wear.
What Are the Regional Differences in User Preferences for EVA Slippers?
1. **Tropical and Subtropical Regions (e.g., Southeast Asia, South America)**
– **Focus**: Waterproof, quick-drying, lightweight, and breathable for hot, humid climates.
2. **Temperate Regions (e.g., Europe, North America, Japan)**
– **Focus**: Comfort, durability, and simplicity for year-round indoor and outdoor use.
3. **Coastal Tourist Areas (e.g., Mediterranean, Caribbean, Australia)**
– **Focus**: Anti-slip, vibrant designs, easy to clean, and portable for beach and poolside wear.
4. **Middle East and North Africa**
– **Focus**: Breathable and comfortable, with some preferring closed-toe designs and warm colors.
5. **Urban Areas (e.g., New York, Tokyo, Seoul)**
– **Focus**: Stylish, functional, trend-oriented designs suitable for daily wear and commuting.
6. **Rural and Natural Settings**
– **Focus**: Durable, easy-to-clean, anti-slip, with practical and long-lasting features for varied terrain.
What Are the Current Design Trends for EVA Slippers?
1. **Minimalist Design**
– **Trend**: Simple, versatile silhouettes with muted colors for everyday wear.
2. **Thick Soles and Cushioning**
– **Trend**: Chunky soles for added height and comfort, aligning with “chunky” fashion.
3. **Bold and Gradient Colors**
– **Trend**: Vibrant, gradient hues for a standout, summer-ready look.
4. **Enhanced Anti-Slip and Waterproof Features**
– **Trend**: Improved grip and water-resistant materials for safety and usability.
5. **Modular and Adjustable Designs**
– **Trend**: Customizable components and adjustable straps for personalized fit.
6. **Eco-Friendly and Sustainable Materials**
– **Trend**: Recyclable and biodegradable EVA options, reflecting eco-conscious choices.
7. **Trendy Collaborations and Customization**
– **Trend**: Brand collaborations and personalization options like colors and engravings for uniqueness.
What Innovative Features in EVA Slippers Are Gaining Popularity?
1. **Massage and Foot Stimulation**
– **Feature**: Sole with raised massage points for improved circulation and foot relaxation.
2. **Eco-Friendly Materials**
– **Feature**: Biodegradable or plant-based EVA to reduce environmental impact.
3. **Antibacterial and Odor Control**
– **Feature**: Antimicrobial agents in EVA to keep slippers hygienic in damp environments.
4. **Adjustable and Modular Design**
– **Feature**: Customizable straps and interchangeable soles for fit and versatility.
5. **Temperature Regulation and Breathability**
– **Feature**: Ventilation holes and temperature-regulating materials for comfort in hot conditions.
6. **Enhanced Shock Absorption and Support**
– **Feature**: Added cushioning or air layers to reduce foot pressure during extended wear.
7. **Compact and Portable Design**
– **Feature**: Foldable or rollable construction, ideal for travel and easy storage.
Which Brands Are Innovating in EVA Slipper ?
1. **Crocs**
– **Innovation**: Croslite™ material for comfort and support; popularized through fashion-forward collaborations.
2. **Birkenstock**
– **Innovation**: Ergonomic EVA designs for water resistance and comfort, blending classic style with functionality.
3. **HOKA ONE ONE**
– **Innovation**: Thick soles and Meta-Rocker technology for post-activity recovery, ideal for support and shock absorption.
4. **OOFOS**
– **Innovation**: OOfoam™ material to reduce impact, catering to recovery and foot health.
5. **Adidas (Adilette Series)**
– **Innovation**: Cloudfoam and lightweight EVA for softness and support, with trend-driven collaborations.
6. **Nike (Victori Series)**
– **Innovation**: EVA and foam blend for cushioning; integrates sportswear aesthetics into casual wear.
7. **Teva**
– **Innovation**: Anti-slip, antimicrobial EVA designs suited for outdoor exploration and water use.
Customization
Can EVA Slippers Be Fully Customized in Color and Pattern?
Yes!
1. **Dip Dyeing**
– **Features**: Dips EVA in dye for even color coverage; ideal for simple, large-area single-tone coloring.
– **Benefits**: Cost-effective, durable, and suitable for consistent color customization.
2. **Heat Transfer Printing**
– **Features**: Uses heat to transfer intricate designs from paper to EVA; supports multi-color, gradient, and detailed patterns.
– **Benefits**: Delivers vibrant, long-lasting designs; perfect for complex visuals.
3. **Screen Printing**
– **Features**: Presses ink through a screen onto EVA; suited for single or simple multi-color logos or patterns.
– **Benefits**: Low-cost and stable colors; ideal for large batches with basic designs.
4. **Inkjet Printing**
– **Features**: Directly prints high-definition images on EVA; flexible for small runs and detailed customization.
– **Benefits**: Offers sharp, vivid colors and customization; less durable than other methods.
5. **Embossing**
– **Features**: Uses molds to create raised, textured patterns; enhances logo or design details.
– **Benefits**: Adds a tactile, durable finish, providing texture and a premium look.
6. **Water Transfer Printing**
– **Features**: Transfers patterns using water as a medium; allows full-coverage, complex designs on EVA.
– **Benefits**: Bright, detailed, and widely applicable; excellent for extensive pattern coverage.
Can EVA Slippers Be Customized with Multicolor or Gradient Effects?
Yes!
1. **Heat Transfer Printing**
– **Feature**: Transfers complex multi-color or gradient designs with heat.
– **Benefit**: Vivid and durable colors, ideal for mass customization.
2. **Inkjet Printing**
– **Feature**: High-resolution printing directly on EVA.
– **Benefit**: Flexible for small batches; offers rich color layering.
3. **Water Transfer Printing**
– **Feature**: Uses water as a medium for full-coverage gradients.
– **Benefit**: Subtle gradients and high durability; ideal for intricate designs.
4. **In-Mold Decoration (IMD)**
– **Feature**: Embeds colors and gradients during molding.
– **Benefit**: Long-lasting and fade-resistant, suitable for heavy use.
5. **Multicolor EVA Lamination**
– **Feature**: Layers different EVA colors to create natural gradients.
– **Benefit**: Consistent, durable colors; ideal for natural gradient effects.
Can EVA Slippers Be Freely Customized in Style, Shape, and Size?
Yes!
1. **Style Customization**
– **Options**: Flexible for different styles (e.g., slides, flip-flops).
– **Limitations**: Custom styles may increase mold costs, especially for small batches.
2. **Shape Customization**
– **Options**: Customizable arch support, sole thickness, and foot shape adaptation.
– **Limitations**: Unique shapes require specialized molds, best for large orders.
3. **Size Customization**
– **Options**: Standard size ranges with options for extended sizing.
– **Limitations**: Individual size molds increase costs; best suited for bulk production.
4. **Additional Personalization**
– **Options**: Colors, patterns, and logos can be added for branding or personalization.
– **Limitations**: Small batches with complex designs may raise production costs.
Can Specific Features (e.g., Anti-Slip, Waterproof, Antibacterial) Be Added to EVA Slippers?
Yes!
1. **Anti-Slip**
– **Implementation**: Special sole textures or rubber layers for better grip.
– **Best Use**: Suitable for wet areas like bathrooms and pools.
2. **Waterproof**
– **Implementation**: EVA’s natural water resistance or additional waterproof coatings.
– **Best Use**: Ideal for beach or poolside wear to prevent water absorption.
3. **Antibacterial**
– **Implementation**: Antimicrobial additives or coatings in EVA material.
– **Best Use**: Enhances hygiene in gyms, bathrooms, and shared spaces.
4. **Shock Absorption and Support**
– **Implementation**: Added cushioning or air pockets in the sole.
– **Best Use**: Reduces foot fatigue for prolonged wear.
5. **Breathability**
– **Implementation**: Ventilation holes or breathable materials.
– **Best Use**: Keeps feet dry and comfortable, especially in warm climates.
Can Brand Logos, Text, or Designs Be Customized on EVA Slippers?
Yes!
1. **Heat Transfer Printing**
– **Feature**: Transfers multi-color, intricate designs.
– **Benefit**: Vivid and durable, ideal for large batches.
2. **Screen Printing**
– **Feature**: Prints simple logos or text using ink.
– **Benefit**: Cost-effective, suitable for single or basic color designs.
3. **Laser Engraving**
– **Feature**: Engraves logos/text directly onto EVA.
– **Benefit**: Permanent and refined, adds a premium feel.
4. **Embossing and Debossing**
– **Feature**: Creates raised or recessed logos.
– **Benefit**: Durable with a high-quality tactile finish.
5. **Embroidered Patches**
– **Feature**: Adds sewn or heat-pressed logo patches.
– **Benefit**: Stylish and dimensional, great for trendy designs.
What Should Be Considered for Custom Printing
1. **Printing Technique Selection**
– **Consideration**: Choose a method (e.g., heat transfer, screen printing) based on color complexity and durability needs.
2. **Pattern Durability**
– **Consideration**: Ensure the technique resists wear, washing, and sunlight; heat transfer is often more durable.
3. **Color Accuracy**
– **Consideration**: EVA material may alter color slightly; test samples for best color match.
4. **Material Compatibility**
– **Consideration**: Ensure ink adheres well to EVA, especially if the surface is smooth or porous.
5. **Water and UV Resistance**
– **Consideration**: For outdoor use, select water- and UV-resistant inks to prevent fading.
6. **Resolution and Clarity**
– **Consideration**: Use high-resolution designs to ensure clear, detailed prints.
Can EVA Slipper Packaging Be Customized?
Yes!
1. **Packaging Material**
– **Options**: Choose from paper boxes, plastic bags, eco-friendly materials.
– **Suggestion**: For sustainable branding, use biodegradable or recycled materials.
2. **Size and Structure**
– **Options**: Custom sizing for a snug fit; structures like window boxes or foldable designs.
– **Suggestion**: Ensure durability and consider reusable or collapsible options.
3. **Brand Logo and Design**
– **Options**: Add logos, colors, and patterns to enhance brand recognition.
– **Suggestion**: Focus on quality printing for a professional brand image.
4. **Eco-Friendly Choices**
– **Options**: Recyclable, biodegradable, or reusable materials.
– **Suggestion**: Ideal for eco-conscious consumers and sustainable branding.
5. **Additional Features**
– **Options**: Add handles, tags, or hangers for convenience and extra branding.
– **Suggestion**: Enhance user experience, making packaging part of the product appeal.
What Is the Production Lead Time for Custom EVA Slippers?
1. **Order Quantity**
– **Small Orders**: Typically 1-3 weeks.
– **Large Orders**: May extend to 4-8 weeks.
2. **Design Complexity**
– **Simple Designs**: 1-2 weeks.
– **Complex Customizations**: 3-6 weeks due to specialized molds or multicolor prints.
3. **Material and Mold Preparation**
– **Standard Materials**: Quick start with minimal delay.
– **Special Materials/Molds**: Adds 1-2 weeks for sourcing or custom molds.
4. **Production and Printing Processes**
– **Standard Techniques**: Shorter timeline.
– **Advanced Techniques**: Adds 1-2 weeks for detailed work like embossing or multi-color printing.
5. **Quality Control and Packaging**
– **Standard QC and Packaging**: Minimal impact.
– **Custom Packaging/Extended QC**: Adds 3-5 days.
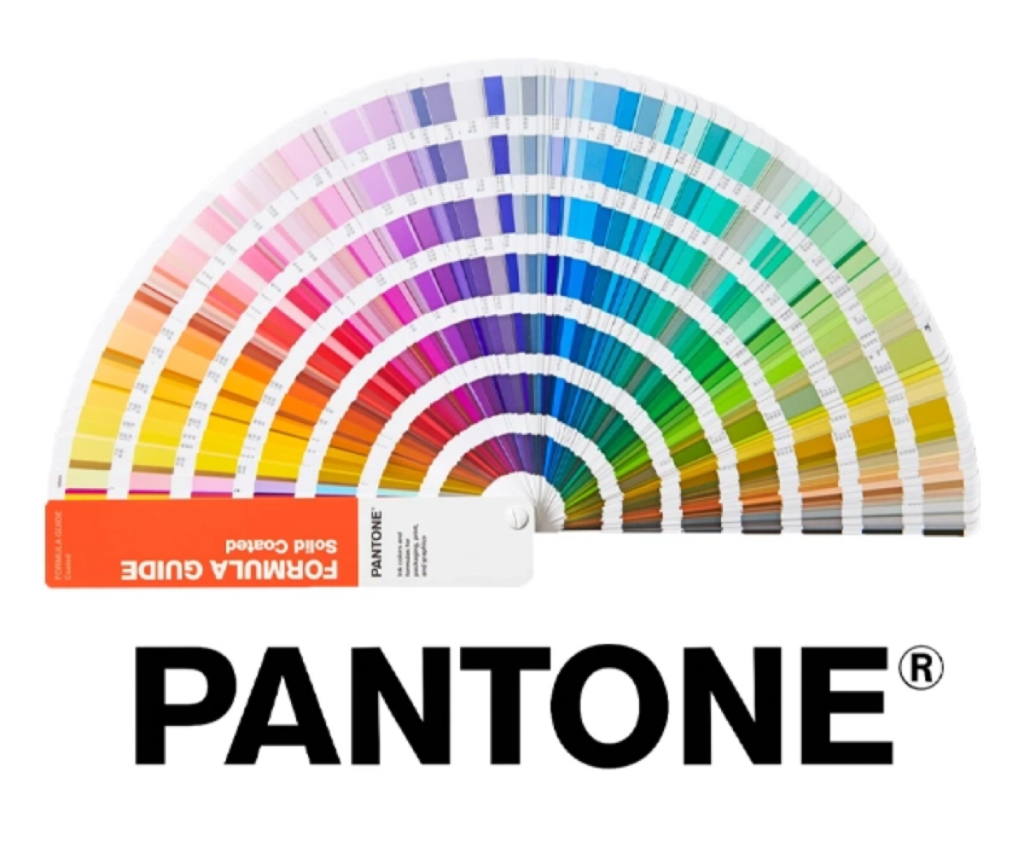
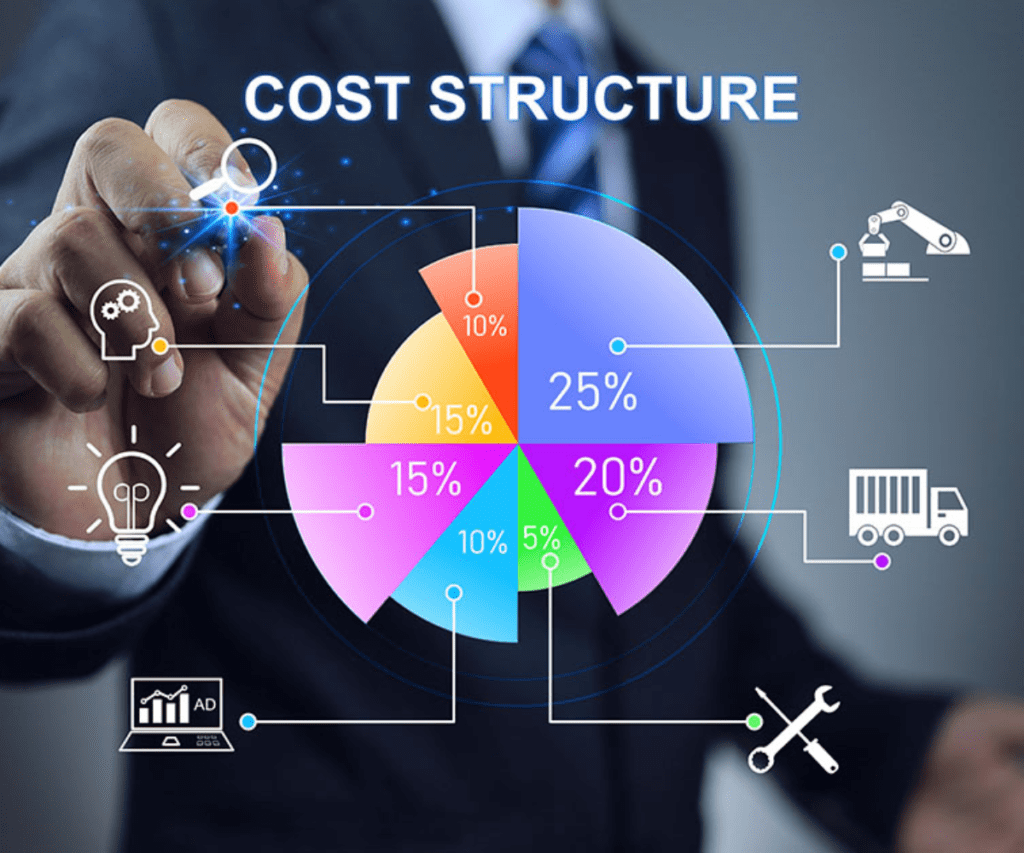
Price Struceture
What Percentage of EVA Slipper Raw Material Costs?
**Raw Material**
– **Range**: EVA material typically accounts for 30%-50% of total production costs.
– **Factors**: Design and material usage affect EVA’s proportion in overall costs.
What Proportion of Production Costs?
1. **Injection Molding**
– **Cost Share**: 40%-60% of total production costs.
– **Factors**: High initial mold costs but efficient for large-scale, detailed production.
2. **Compression Molding**
– **Cost Share**: 30%-50% of production costs.
– **Factors**: Lower mold cost, more labor-intensive, suitable for small batches and thicker designs.
3. **Foaming**
– **Cost Share**: 20%-40% of production costs.
– **Factors**: Low material cost due to expansion; ideal for lightweight, cushioned designs.
What Is the Estimated Energy Cost (Electricity, Fuel) per Pair ?
1. **Electricity Consumption**
– **Injection Molding**: Approx. $0.05 – $0.1 per pair.
– **Compression Molding**: Approx. $0.08 – $0.12 per pair.
– **Foaming**: Approx. $0.03 – $0.07 per pair.
2. **Fuel Consumption (If Applicable)**
– **Estimate**: Around $0.02 – $0.05 per pair, depending on heating needs.
3. **Cost Influencing Factors**
– **Production Volume**: Higher volumes reduce per-unit energy cost.
– **Equipment Efficiency**: Newer, efficient machinery lowers energy consumption.
– **Process Type**: Injection and foaming typically consume less energy than compression molding.
What Percentage of Labor Costs?
1. **Cost Percentage by Process**
– **Injection Molding**: 10%-20% due to high automation.
– **Compression Molding**: 20%-30% with more manual operations.
– **Foaming**: 15%-25% with moderate automation needs.
2. **Automation Impact**
– **Higher Automation**: Reduces labor costs significantly.
– **Manual Operations**: Increase labor cost share.
3. **Regional Labor Cost Variations**
– **High-Cost Regions**: Labor share higher in areas like North America and Europe.
– **Low-Cost Regions**: Lower labor share in regions like Southeast Asia.
What Are the Purchase Costs, Depreciation Period, and Maintenance Expenses for Equipment?
1. **Purchase Costs**
– **Injection Equipment**: $20,000 – $50,000.
– **Compression Equipment**: $10,000 – $30,000.
– **Foaming Equipment**: $15,000 – $40,000.
2. **Depreciation Period**
– **Typical Range**: 5-10 years, depending on usage frequency and equipment durability.
3. **Maintenance Expenses**
– **Annual Cost**: 3%-5% of equipment price for routine maintenance and parts replacement.
4. **Overall Annual Operating Cost**
– **Estimate**: Approximately 10%-15% of purchase cost, combining depreciation and maintenance.
What Are the Logistics Costs from Raw Materials to Finished EVA Slippers?
1. **Raw Material Transport**
– **Cost Share**: 10%-20% of total logistics costs.
– **Factors**: Distance to production site and transport mode affect costs.
2. **Finished Product Storage**
– **Cost Share**: 5%-10%.
– **Factors**: Warehouse rental, turnover rate, and inventory management.
3. **Finished Product Transport**
– **Cost Share**: 60%-80%, the largest logistics cost.
– **Factors**: Destination distance and shipping method (sea, air, land).
4. **Packaging and Handling**
– **Cost Share**: 5%-10%.
– **Factors**: Packaging type and manual vs. automated handling.
5. **Overall Estimate**
– **Total Cost Impact**: Logistics generally comprise 10%-20% of total production costs.
What Percentage of quality Inspection and Control Cost?
1. **Massage and Foot Stimulation**
– **Feature**: Sole with raised massage points for improved circulation and foot relaxation.
2. **Eco-Friendly Materials**
– **Feature**: Biodegradable or plant-based EVA to reduce environmental impact.
3. **Antibacterial and Odor Control**
– **Feature**: Antimicrobial agents in EVA to keep slippers hygienic in damp environments.
4. **Adjustable and Modular Design**
– **Feature**: Customizable straps and interchangeable soles for fit and versatility.
5. **Temperature Regulation and Breathability**
– **Feature**: Ventilation holes and temperature-regulating materials for comfort in hot conditions.
6. **Enhanced Shock Absorption and Support**
– **Feature**: Added cushioning or air layers to reduce foot pressure during extended wear.
7. **Compact and Portable Design**
– **Feature**: Foldable or rollable construction, ideal for travel and easy storage.
What Percentage of Handling Waste and Defective Products Costs?
1. **Cost Percentage**
– **Range**: Typically 1%-5% of total production costs.
2. **Key Factors**
– **Defect Rate**: Higher defect rates increase handling costs.
– **Processing Method**: Recycling waste is cheaper; disposal incurs higher fees.
3. **Environmental Compliance**
– **Additional Costs**: Strict regulations may require fees for waste management and safe disposal.
Test & Quality Control
What Are the Quality Control Steps in EVA Slipper Production?
1. **Raw Material Inspection**
– **Process**: Check EVA material for density, elasticity, and color.
– **Purpose**: Ensure consistency and quality before production.
2. **In-Process Control**
– **Process**: Monitor key stages (e.g., molding, foaming) with sample checks.
– **Purpose**: Maintain uniformity and reduce defects during production.
3. **Semi-Finished Product Inspection**
– **Process**: Inspect dimensions and appearance mid-production.
– **Purpose**: Identify and correct issues early.
4. **Finished Product Testing**
– **Process**: Sample testing for durability, slip resistance, and elasticity.
– **Purpose**: Confirm adherence to design and quality standards.
5. **Packaging and Pre-Shipment Check**
– **Process**: Verify packaging integrity and labeling accuracy.
– **Purpose**: Ensure safe transport and compliance with customer requirements.
6. **Periodic Review and Feedback**
– **Process**: Regularly review results and update processes.
– **Purpose**: Continuously improve quality and reduce defect rates.
What Tools and Techniques Are Used to Inspect Quality
1. **Dimensions and Shape**
– **Tools**: Calipers and gauges.
– **Purpose**: Verify length, width, and thickness.
2. **Density and Hardness**
– **Tools**: Density meter, Shore durometer.
– **Purpose**: Ensure consistent weight, density, and elasticity.
3. **Slip Resistance**
– **Tools**: Friction tester, static friction coefficient test.
– **Purpose**: Test grip on wet and dry surfaces for safety.
4. **Abrasion Resistance**
– **Tools**: Abrasion tester, drum wear test.
– **Purpose**: Assess durability under prolonged wear.
5. **Color and Appearance**
– **Tools**: Color comparison lightbox, visual inspection.
– **Purpose**: Ensure color consistency and detect surface defects.
6. **Antibacterial and Water Resistance**
– **Tools**: Antibacterial coating test, water immersion test.
– **Purpose**: Confirm hygiene standards and waterproofing.
What Domestic and International Standards for Quality Testing?
1. **ISO Standards**
– **Examples**: ISO 13287 (Slip resistance), ISO 17707 (Abrasion resistance), ISO 16187 (Antibacterial testing).
2. **ASTM Standards**
– **Examples**: ASTM D2240 (Hardness), ASTM F2913 (Slip resistance), ASTM G154 (UV resistance).
3. **GB Standards (China)**
– **Examples**: GB/T 3903.3 (Abrasion), GB/T 2828.1 (Sampling inspection), GB 30585 (Children’s safety).
4. **EN Standards (EU)**
– **Examples**: EN ISO 20347 (Durability and safety), EN 13287 (Slip resistance).
5. **Environmental and Chemical Safety**
– **Examples**: REACH (EU chemical safety), ROHS (Hazardous substances).
What Are the Specific Testing Standards for Slip Resistance, Abrasion, Softness, and Aging Resistance?
1. **Slip Resistance**
– **Standards**: ISO 13287 / EN 13287, ASTM F2913.
– **Requirements**: Minimum friction coefficient of 0.3-0.6 on wet/dry surfaces.
2. **Abrasion Resistance**
– **Standards**: ISO 17707, GB/T 3903.3.
– **Requirements**: Wear depth not exceeding 2mm in durability tests.
3. **Softness (Hardness)**
– **Standards**: ASTM D2240 (Shore A hardness), ISO 868.
– **Requirements**: Hardness range of 45-65 Shore A for comfort and elasticity.
4. **Aging Resistance**
– **Standards**: ASTM G154, ISO 4892.
– **Requirements**: Material should maintain color, resist cracking, and avoid deformation under UV and humidity exposure.
How Are Color Fastness and Chemical Resistance Tested to Ensure Durability?
1. **Color Fastness Tests**
– **Water Wash Fastness**:
– **Method**: ISO 105-C06 or AATCC 61; submerge slippers in washing solution to simulate repeated washing.
– **Requirement**: No significant color change, ideally rated 1-5 (5 being best).
– **Abrasion Fastness**:
– **Method**: ISO 105-X12 or AATCC 8; dry and wet rubbing with abrasion tester.
– **Requirement**: Colorfastness rating of 3 or above, ensuring durability with wear.
– **Light Fastness**:
– **Method**: ISO 105-B02 or AATCC 16; expose to artificial light to assess UV impact.
– **Requirement**: Stability of 3+ on scale, avoiding noticeable fading with sunlight exposure.
2. **Chemical Resistance Tests**
– **Acid and Alkali Resistance**:
– **Method**: ISO 16750 or ASTM D543; submerge in acid/alkaline solutions to simulate exposure.
– **Requirement**: No discoloration, swelling, or structural damage.
– **Oil Resistance**:
– **Method**: ASTM D471; immerse in oil-based chemicals to mimic oil contact.
– **Requirement**: Minimal swelling or hardness change, maintaining durability against oil.
– **Detergent Resistance**:
– **Method**: Wipe surface with cleaning agents to observe color and material response.
– **Requirement**: No visible color change or softening, ensuring resilience to cleaning products.
What Physical Performance Tests Are Conducted on EVA Slippers?
1. **Slip Resistance**
– **Method**: ISO 13287 or ASTM F2913; friction testing on wet and dry surfaces.
– **Purpose**: Ensure adequate grip under various conditions for wearer safety.
2. **Abrasion Resistance**
– **Method**: ISO 17707 or GB/T 3903.3; simulate long-term wear with rotating abrasive wheels.
– **Purpose**: Assess durability of sole material under extended use.
3. **Flexibility and Bending Strength**
– **Method**: Bend tests per ISO 24233 to simulate repetitive bending during wear.
– **Purpose**: Confirm sole flexibility without cracking, ensuring comfort and longevity.
4. **Hardness and Softness**
– **Method**: ASTM D2240 Shore A hardness test.
– **Purpose**: Measure material softness for comfort, targeting optimal Shore A range.
5. **Aging and UV Resistance**
– **Method**: ASTM G154 or ISO 4892; UV exposure and heat cycles.
– **Purpose**: Evaluate color stability and material integrity under sun exposure.
6. **Compression Set**
– **Method**: ISO 815; measure material deformation after compression.
– **Purpose**: Ensure cushioning retains shape and effectiveness over time.
How Is the Stability of EVA Slippers Tested Under Extreme Conditions?
1. **High Temperature Durability**
– **Method**: ISO 188 or ASTM D573; place slippers in a heated chamber at 50°C-70°C for 24-48 hours.
– **Purpose**: Check for deformation, color stability, and resilience in hot environments.
2. **Low Temperature Resistance**
– **Method**: ISO 812 or ASTM D2137; store in -20°C to -40°C conditions for 24 hours.
– **Purpose**: Ensure flexibility and resistance to cracking in cold climates.
3. **Humidity Resistance**
– **Method**: ISO 483 or ASTM D618; maintain at 90%-95% humidity, 25°C-40°C for 72 hours.
– **Purpose**: Verify stability, water resistance, and mold prevention in humid environments.
4. **UV Aging Resistance**
– **Method**: ASTM G154 or ISO 4892; expose to UV light for 48-72 hours.
– **Purpose**: Assess color retention and surface integrity in sunlight exposure.
5. **Water Immersion Stability**
– **Method**: ISO 5423; fully submerge slippers in water for 24 hours.
– **Purpose**: Test waterproofing and dimensional stability after prolonged water exposure.
#What Chemical Substance Limits Must Meet for Safety Compliance ?
1. **REACH Standard (EU)**
– **Substances**: SVHCs including phthalates, heavy metals.
– **Limits**: Phthalates ≤ 0.1%, heavy metals (e.g., lead, cadmium) ≤ 0.01%-0.1%.
– **Purpose**: Protects consumer health by limiting toxic substances.
2. **ROHS Directive (EU)**
– **Substances**: Lead, mercury, cadmium, hexavalent chromium.
– **Limits**: ≤ 0.1%-0.01% depending on substance.
– **Purpose**: Ensures environmental friendliness and safety.
3. **California Proposition 65 (US)**
– **Substances**: Carcinogens, reproductive toxins like phthalates.
– **Requirement**: Warning labels for potentially harmful substances.
– **Purpose**: Informs consumers of chemical exposure risks.
4. **GB 30585-2014 (China)**
– **Substances**: Formaldehyde, heavy metals.
– **Limits**: Formaldehyde ≤ 75 mg/kg, heavy metals per standard values.
– **Purpose**: Ensures child safety in footwear products.
5. **Other Restricted Substances**
– **Examples**: PAHs (≤ 1 mg/kg), azo dyes (≤ 30 mg/kg).
– **Purpose**: Reduces risks from carcinogenic and toxic compounds.
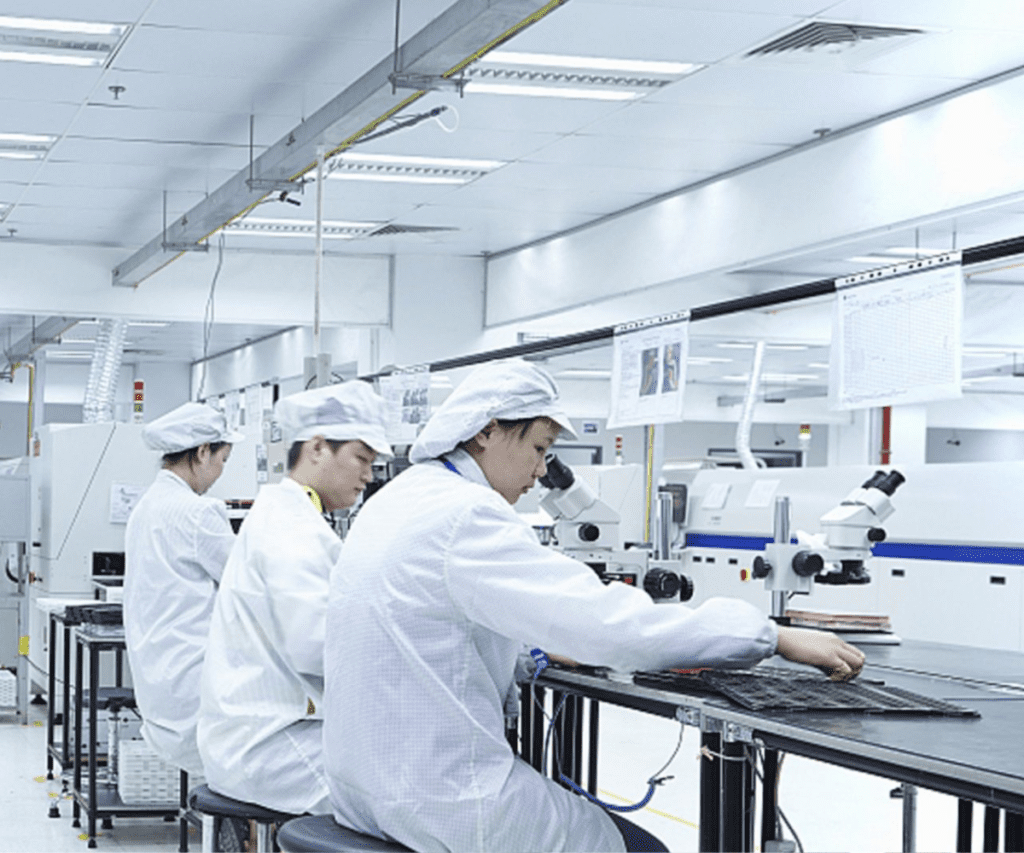